TOP
STM32H753BIT6
MCU 32-Bit STM32 ARM Cortex M7 RISC 2MB Flash 1.8V/2.5V/3.3V 208-Pin LQFP Tray
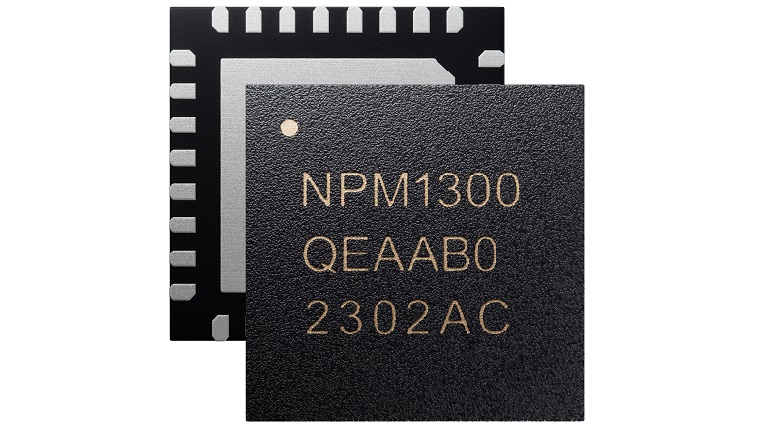
- Manufacturer Lead Time
- Minimum
- Country Of Origin
- HTSN
- Ships from
Technical Attributes
Key Features
- ROP, PC-ROP, active tamper, secure firmware upgrade support, Secure access mode
General-purpose input/outputs
- Up to 168 I/O ports with interrupt capability
- Fast I/Os capable of up to 133 MHz
- Up to 164 5 V-tolerant I/Os
Reset and power management
- 3 separate power domains which can be independently clock gated or switched off to maximize power efficiency:
- D1: high-performance capabilities for high bandwidth peripherals
- D2: communication peripherals and timers
- D3: reset/clock control/power management
- POR, PDR, PVD and BOR
- Embedded regulator (LDO) with configurable scalable output to supply the digital circuitry
- Voltage scaling in Run and Stop mode (5 configurable ranges)
- Backup regulator (~0.9 V)
- Voltage reference for analog peripheral/VREF+
- Low-power modes: Sleep, Stop, Standby and
VBAT supporting battery charging
Low-power consumption
- Low-power consumption
Clock management
- Internal oscillators: 64 MHz HSI, 48 MHz HSI48, 4 MHz CSI, 40 kHz LSI
- External oscillators: 4-48 MHz HSE, 32.768 kHz LSE
- 3× PLLs (1 for the system clock, 2 for kernel clocks) with fractional mode
Interconnect matrix
- 3 bus matrices (1 AXI and 2 AHB)
- Bridges (5× AHB2-APB, 2× AXI2-AHB)
4 DMA controllers to unload the CPU
- 1× high-speed general-purpose master direct memory access controller (MDMA) with linked list support
- 2× dual-port DMAs with FIFO and request router capabilities
- 1× basic DMA with request router capabilities
Up to 35 communication peripherals
- 4× I2C FM+ interfaces (SMBus/PMBus)
- 4× USART/4x UARTs (ISO7816 interface, LIN, IrDA, modem control, up to 12.5 Mbit/s) and 1x LPUART
- 6× SPIs, including 3 with muxed duplex I2S audio class accuracy via internal audio PLL or external clock, 1x I2S in LP domain (up to 133 MHz)
- 4x SAIs (serial audio interface)
- SPDIFRX interface
- SWPMI single-wire protocol master I/F
- MDIO Slave interface
- 2× SD/SDIO/MMC interfaces (up to 125 MHz)
- 2× CAN controllers: 2 with CAN FD, 1 with time-triggered CAN (TT-CAN)
- 2× USB OTG interfaces (1FS, 1HS/FS)
- Ethernet MAC interface with DMA controller
- HDMI-CEC
- 8- to 14-bit camera interface (up to 80 MHz)
11 analog peripherals
- 3× ADCs with 16-bit max. resolution (14 bits 4 MSPS, 16 bits 3.6 MSPS)
- 1× temperature sensor
- 2× 12-bit D/A converters (1 MHz)
- 2× ultra-low-power comparators
- 2× operational amplifiers (8 MHz bandwidth)
- 1× digital filters for sigma delta modulator (DFSDM) with 8 channels/4 filters
Graphics
- LCD-TFT controller up to XGA resolution
- Chrom-ART graphical hardware Accelerator (DMA2D) to reduce CPU load
- Hardware JPEG Codec
Up to 22 timers and watchdogs
- 1× high-resolution timer (2.5 ns max resolution)
- 2× 32-bit timers with up to 4 IC/OC/PWM or pulse counter and quadrature (incremental) encoder input (up to 200 MHz)
- 2× 16-bit advanced motor control timers (up to 200 MHz)
- 10× 16-bit general-purpose timers (up to 200 MHz)
- 5× 16-bit low-power timers (up to 200 MHz)
- 2× watchdogs (independent and window)
- 1× SysTick timer
- RTC with sub-second accuracy & HW calendar
Cryptographic acceleration
- AES 128, 192, 256, TDES
- HASH (MD5, SHA-1, SHA-2), HMAC
- True random number generators (3 oscillators each)
Debug mode
- SWD & JTAG interfaces
- 4 Kbyte Embedded Trace Buffer
Solderability Test
Prevent assembly problems and storage difficulties.
The solderability of your components determines potential IC or PCB failures and the overall quality of your product. Solderability tests are used to determine the wettability of the connections and their connectivity. They also provide information about their heat resistance and shelf life.
Solderability test approach follows the IPC standard for solderability testing to ensure accurate test results. Components under test undergo a comprehensive process from preconditioning to actual testing, evaluation and reporting. The entire control process is based on the AS6081 protocol and the J-STD-002D standard.
X-ray Analysis
X-ray analysis is a useful, non-destructive process that allows us to examine a component’s interior structure, including any wire bonding, foreign material, unusual voids, or other possible abnormalities. The interior is also compared to and tested among others from the same batch to ensure uniformity and structural integrity.
Choose Tonsin
Consult Your 7x24hours Experts
With skillful members for motherboard hardware engineers, BIOS software engineers,structural engineers , application design engineers and the complete testing process. Tonsin Solution aimed to be the most reliable solution company.
Don’t hesitate to contact us. Tonsin’s product specialists are very happy to help you and provide a variety of flexible and reliable solutions to help you solve various problems.